Custom Schunk
Robotic Gripper Fingers
Getting the right set of robotic gripper fingers for Schunk gripper modules is easy with GripShape. Save design time and manufacturing costs by starting with a pair of standard in-stock gripper finger blanks, use the free online design tool to configure a set of Schunk fingers in minutes, or reach out to one of our experts that will create a custom gripper design for you same day.
Designing optimized gripper tooling is difficult and having optimized gripper fingers can make the difference in the success of your automation project. GripShape’s engineers have created the most comprehensive system of products and services aimed specifically at the point of contact with the workpiece. You can count on us to increase your bottom line by delivering quality, precision products that work the first time.
Start Designing Now
GripShape’s Online Design Tool
Designing custom robotic tooling can be challenging. GripShape’s engineers have created a way to visualize the fingers on the module in real time during the process and it starts by selecting the specific Schunk module from the dropdown and the intuitive CAD configurator automatically generates a set of fingers around the workpiece. Fine tune the configuration with simple to use inputs and GripShape will update the finger geometry using powerful algorithms based on Schunk data. Download the CAD model or have us quickly manufacture the parts for you.
Schunk Pneumatic Grippers
Pneumatic grippers use compressed air to drive a cylinder mechanism inside the gripper body, translating the motion to open and close the jaws. The wide availability of compressed air on most facilities and the simple on-off action of the gripper make it a popular choice for industrial applications.
Schunk Electric Grippers
Electric grippers use servos and other style motors to open and close the jaws of the gripper. This allows for precise control over position and the stroke of the gripper when trying to program multiple positions. Some models offer the velocity and acceleration to be customized which would add flexibility to the gripper module making it ideal for varying sized or smaller, delicate parts.
Applications
With custom-designed SMC Gripper fingers, you have an economical option to replacing current grippers that aren’t grasping objects properly: Instead of wasting expensive time and money investigating replacement gripper models, GripShape’s custom design tool can be used to quickly provide gripper finger design options for a wide variety of applications and industries:
Pick and place grippers are perfect high speed, repetitive tasks that are not ideal for human operators. Robots can perform millions of cycles without stopping and complete operations with accuracy and dexterity that are hard to achieve otherwise. Pick and place robots are very flexible and used in conveyor systems, cells, production and packaging line set ups.
Machine Tending robots move parts or products from a staging position and orient them in a way that they can then interact with the machine and then remove the part once the operation is complete. These robots tend to provide more complex movements and capabilities than other more basic material handling applications which make them ideal for industrial automation. The repeatability, long run times and accuracy are the main reasons machine tending robots are deployed to reduce costs.
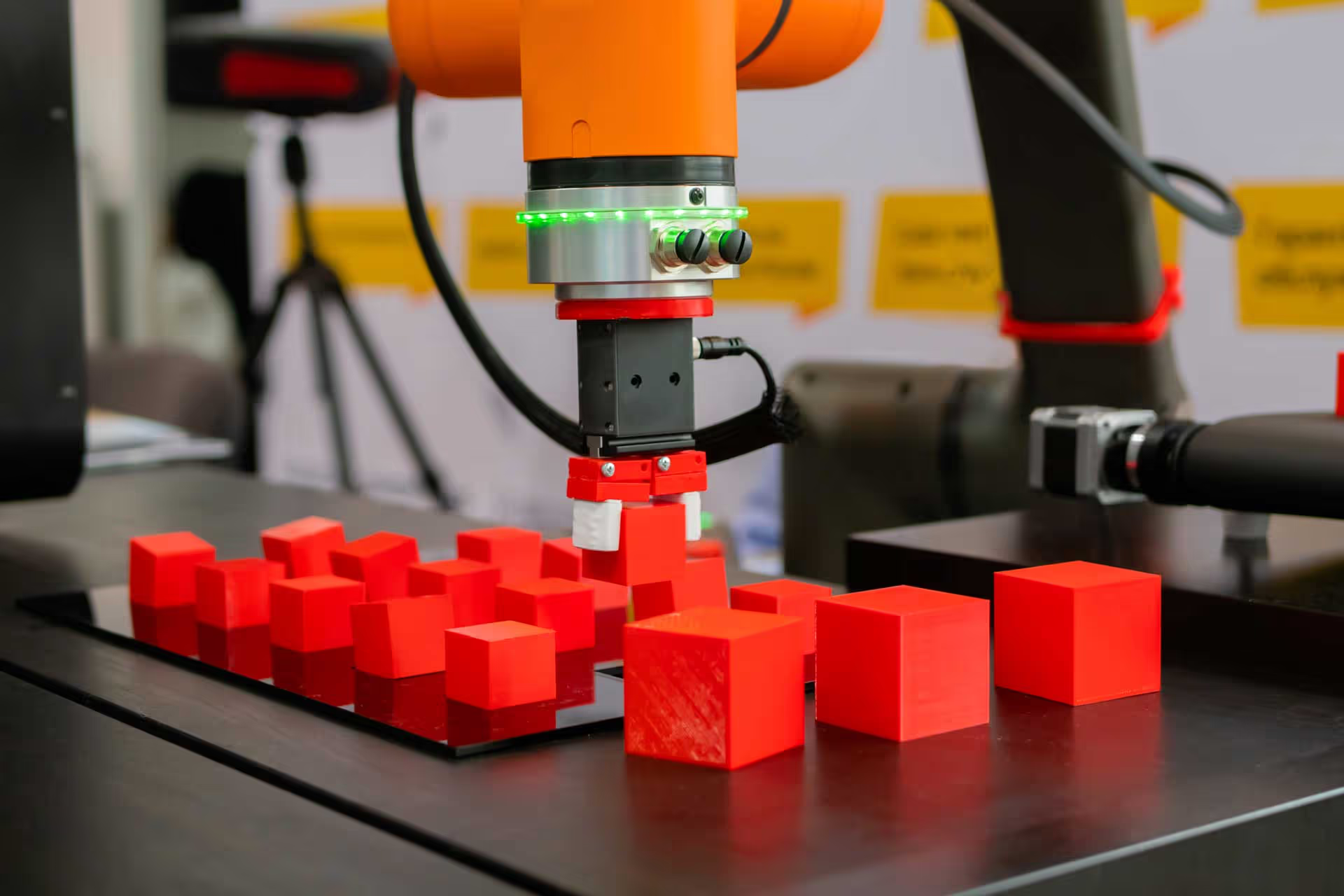
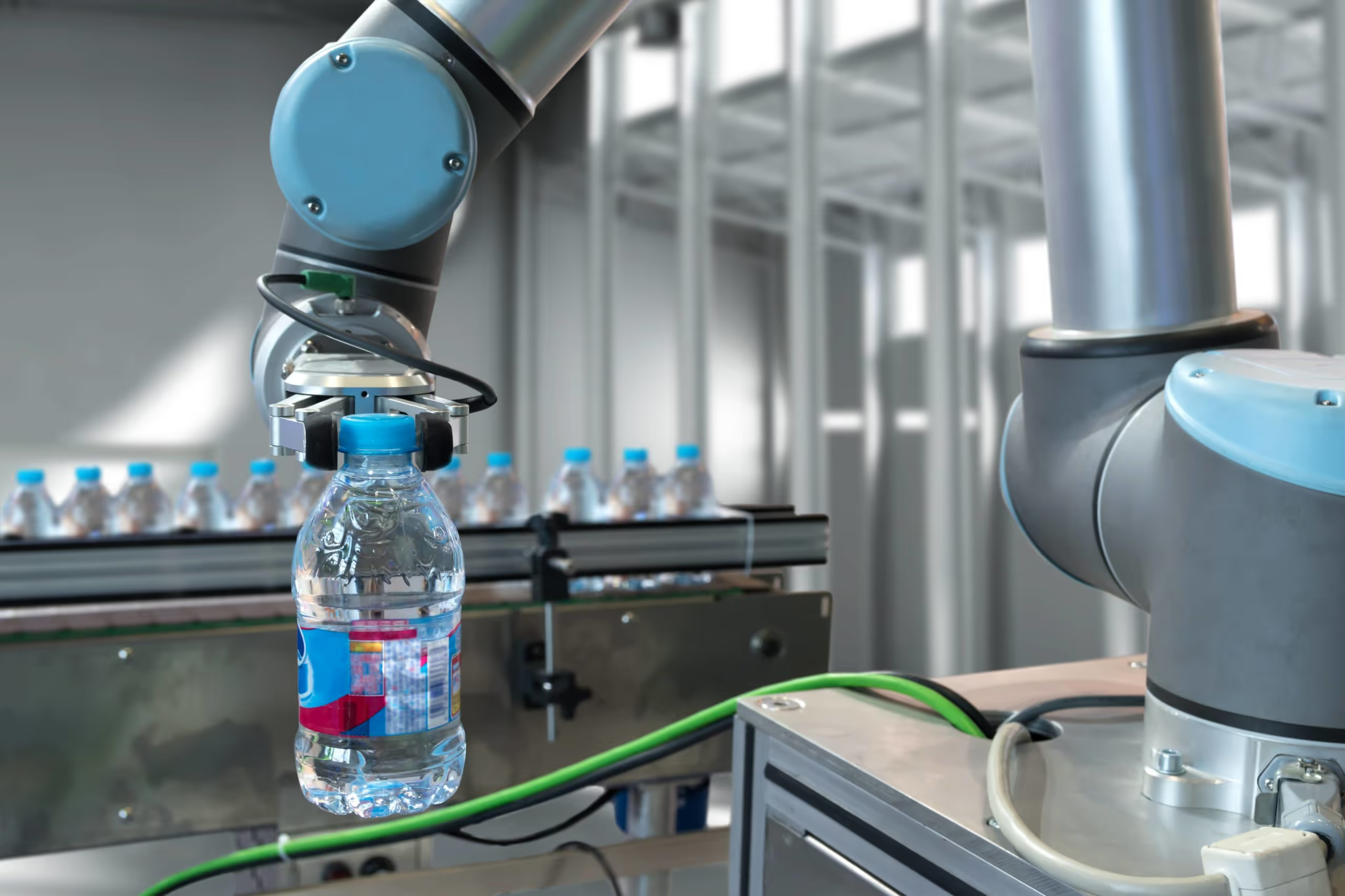
Product assembly lines often use robotic grippers to insert, verify or even fasten parts into production components or assemblies. The reliability, precision and safety are benefits to using automation for assembly. With the cost of automation equipment becoming more affordable, smaller manufacturers are opting to use robotics in their production lines to increase output while maintaining high quality standards.
Material Handling automation systems create efficiency by transporting parts or products at scale. The increase in productivity is due to the speed of the robots, running cycles for long periods of time with no need to stop, reliability and reducing risk associated with material handling. They generally interface with other equipment including conveyors, collision detection systems, containers, automated retrieval systems and carousels. Material handling robots are extremely flexible and can even be redeployed to other areas of the factory if production changes are needed.
Cleanroom environments are used in specialized industrial production or research and have stringent particulate requirements. By using robots, variables can be controlled easily and the greatest contamination risks associated with the projects are greatly reduced. The pharmaceutical and electronics industries rely heavily on automation systems.
Micro gripping is a highly specialized area of automation where very small, fragile workpieces that would be difficult for humans to handle are grasped, transported or inserted into other components. Micro grippers can be difficult to design or manufacture due to the small tooling and expertise required to machine the fingers accurately.
